The Supply Chain Has Changed and What This Means for CDL Drivers
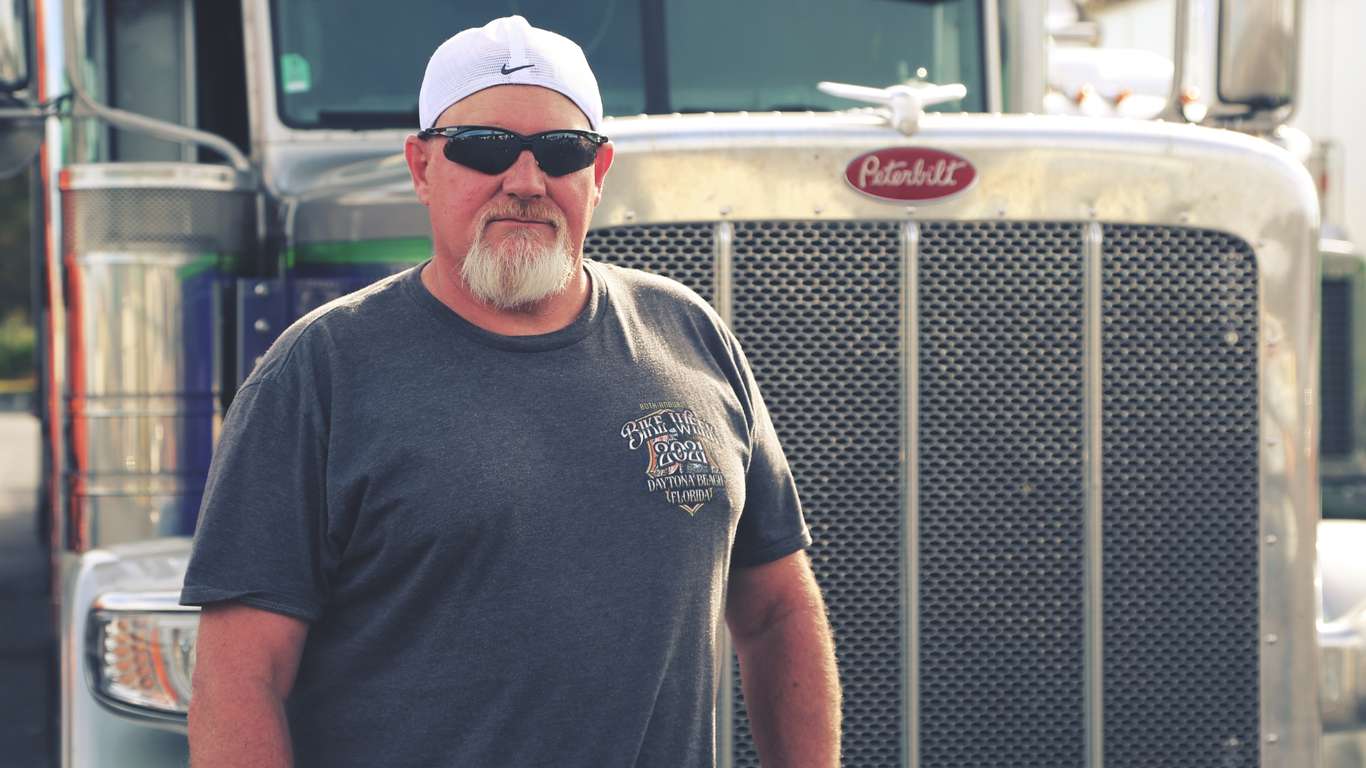
The recent years have revealed just how fragile the global supply chain is. Backlogged ports, massive bottlenecks, and overloaded fulfillment centers are putting tremendous pressure on truck drivers.
Drivers are feeling the pressure to deliver faster, drive longer, and do it all cheaper than ever before.
This is a pivotal time for trucking - and what happens now will determine the future of how much truck drivers get paid, how they're treated, and how often they get home. Finding a solution that will empower drivers and repair the industry is more important now than it's ever been.
I’m here to break down what’s been happening in the global supply chain to give you a better understanding of how to navigate the new challenges presented during these times.
Next day delivery
The convenience and ever increasing speed of eCommerce – being able to order something and get it delivered the next day has obscured the complex global chain of labor behind it.
The reality behind that convenience is one of the most complicated feats of human coordination we've ever accomplished.
The pandemic, despite predictions by financial experts, caused people to buy more and left the world unable to keep up.
Expecting the global supply chain to miraculously recover while keeping up the same habits that made it burn out in the first place is going to prove challenging. Instead, we may need to radically challenge our habits and expectations.
Bottlenecks: A consequence of scale
To meet the demands of consumers and stay profitable, container ships have been getting larger and larger. One standard container ship moving items from Asia across the pacific is as big as a skyscraper laid on its side. These massive containers may be more efficient at moving unfathomable amounts of cargo, but their size can also mean their downfall.
When something goes wrong - say a ship is delayed, or some other unforeseen problem arises like the 2021 Suez Canal Obstruction - the consequences are huge. Much larger than if something were to go wrong with just one “regular sized” ship.
Delays result in massive inefficiency and rapidly accumulating financial loss - not to mention an inability to send containers back home (which drives up the price of all remaining containers and makes delivery).
The same potential for failure applies to the world's ports. California, for instance, is a port that has become bigger and bigger over the years. The port of LA represents 40% of all US imports, and 30% of US exports.
When the world's largest ports become centralized and massive, the world relies on them more. Inefficiencies, problems, delays, backlogs, then too create huge consequences.
Ports are becoming increasingly monolithic - where a few ports are responsible for so much cargo, that when something goes wrong… it goes seriously wrong. Maybe one of the approaches the US should take in the coming ten years with its huge infrastructure bill is to invest into the creation and development of other viable port locations. One such idea is to develop the port of Texas and increase trade with Mexico.
The problem in L.A.
Before productivity fell sharply, the port of LA processed 900,000 containers monthly. This was an unprecedented and large number compared to years prior, where the number of containers would rarely reach that level.
Additionally, containers that would previously take three days to process, now often take two weeks or more, leading to massive cascades of inefficiency.
The port is operated by a bunch of unions and state agencies, making consensus between all groups very difficult.
Despite what some news outlets would have had you believe, it isn’t a driver shortage issue.
Why keeping ports open 24/7 doesn't work
Biden famously announced that in order to combat the backlog at California's ports, he would make them stay open 24 hours a day. The problem with that line of thinking is that it doesn't take into account the entirety of the supply chain.
Let's say a port makes a container available for pickup at 3 am. A truck driver would have to agree to pick up that load, and then the distribution center would have to also agree to accept the load in the middle of the night. The LA port consequently demands that if a 24/7 solution is to work, the rest of the US supply chain should follow suit. Currently, that isn’t happening on a scale that would ensure the ports are actually productive 24/7.
The next leg of the journey - OTR drivers
When a shipping container loaded truck leaves the port of LA, it usually travels a relatively short way to one of the major distribution centers in the Inland Empire. From there, the rest of the journey is made on the back of a long haul Class A vehicle.
How long the OTR drivers have to sit and wait at this point is up to the efficiency at the distribution center.
This is very important to note - the productivity of the driver at this stage has nothing to do with their own initiative. Because the ports are overloaded, and the fulfillment centers are overloaded, the drivers are likely to experience longer and more inconvenient waiting times now than before.
Maybe there’s a way to hold the fulfillment centers liable for delay costs resulting in truck driver productivity loss at this rate. Without something to compensate for this lost time, drivers can find themselves unpaid and on the clock for enough time to render their
Once the trailer is finally loaded, the OTR truck driver then proceeds to deliver the cargo to one of the many fulfillment centers across the country.
Automation at fulfillment centers has become essential
These fulfillment centers are full of people doing hard physical labor. Because of its reliance on a healthy and active labor force, the fulfillment industry is one that has struggled deeply as the result of the COVID consumerism spike.
In order to keep up with the promises of fast delivery, fulfillment centers find themselves having to rely on more and more automation and robotics.
Automation at fulfillment centers often doubles productivity, and prepares those working there for the challenges of increased consumer and delivery speed demands.
How the tech is implemented matters, as automation can be a double edged sword. It can relieve people of hard physical labor, but it can also force them to be more productive to keep up with the pace set by the highly productive machines.
Implementing technologies have been shown to lead to more turnover and burnout. The turnover at Amazon fulfillment centers has exceeded 150% according to federal labor data. In fact, so many people leave their jobs at Amazon warehouses, that the company has started tracking turnover on a weekly basis - losing (and replacing) over 3% of its warehouse workforce each week – that’s more than double the rate of competing companies and other warehouses.
Cost of fulfillment WILL go up
Work at fulfillment centers is plentiful and workers have a lot of leverage. The fulfillment centers offering the highest pay and the best benefits will win out in the end, and the rest will have to increase wages to stay competitive.
Increased wages at these centers will lead to higher costs for the consumer.
Last mile delivery
Jobs like UPS are known for delivering a highly professional and reliable service while ensuring its drivers and workers are paid well. Unfortunately, the stability and pay offered by UPS is incompatible with the demands for fast and cheap transport.
Companies are turning to contract workers to limit their liability, drive down pay and reduce costs in other ways. Amazon drives most of these gig-based delivery services such as doordash, uber flex, and more. Drivers have to pay for their own gas, maintenance, and many other costs.
Amazon's market share in the last mile delivery (LMD) sector has recently overtaken Fedex, exceeding 20% of all LMD in the country. With that growth has come a similar deregulation and deskilling seen in the long haul trucking industry.
With decreased wages and harsher working conditions, the LMD industry may face a similar shortage to long haul trucking. Speaking of the driver shortage…
The issue with the driver shortage
It's not about a lack of interest or qualification. Many, many people have a CDL but are unwilling to do what the job takes long-term. The truck driver shortage, then, is fundamentally a retention problem.
One of the main arguments for the drop in quality, pay, and working conditions over time is a deregulation of the trucking industry. Steve Viscelli, author of The Big Rig, claims that truck drivers in the 60s and 70s would make some of the highest salaries amongst all blue collar workers. This was due to the industry being almost fully unionized. When you got a great trucking job, you were likely to have stable and high paying employment for life. The industry was deregulated in 1980, and wages and working conditions fell.
10,000,000 people in the US have CDLs, whereas only 3,500,000 are actively driving. This should indicate the churn in the industry, and the true nature of the “driver shortage” problem.
If things continue at this rate, we’ll be looking at total paralysis of the trucking industry within 10 years. Aging population, unable to replace with new talent, increase in eCommerce and a much larger reliance on long haul trucking. Things have to change, and will - if the industry is to continue serving the needs of the future. This is, hopefully, a very good thing.
The time to change the trucking industry is now
You - the drivers of America - deserve to be treated like the competent, essential professionals you are. To get rewarded for the sacrifices you make. To get benefits, fair wages, and a work environment where your personal needs are respected.
Your ability to find the jobs you want will not only decide the future of your career, but the future of the industry. Your ability to find the jobs you want, on your terms, will decide how companies act, what they pay, and how accountable they are.
That's why Lanefinder exists. We deliver you the best jobs - real trucking jobs presented with trust and transparency. We deliver a platform where companies are held accountable for their promises. We do this out of respect for you, your future, and the future of the industry. Years from now, we don't want to see an industry made up of replaceable steering wheel holders - We want to see an industry of respected, represented, and professional drivers.